The chamfers facilitate assembly and protect the Oring from damage during the installation process The Oring and all surrounding parts should be well lubricated before assembly, preferably with the same fluid as used in the hydraulic system, ensuring compatibility with seals and cylinder components Extrusion gaps and backup ringsThis interactive guide helps you determine the chemical properties, temperature ranges and key uses of chemicals in ORing and seal productionAn Oring seal is one of the most widely used seal to block the clearance gap in the industry today It is also known as toroidal seal Oring seals are used in applications, ranging from garden hose couplings to aerospace or oil and gas duties due to the following advantages Wide application range (pressures, tolerances, temperatures, media)
Www Parker Com Literature O Ring division literature Parker Techseal Radial seal design guide Tsd 5440 Pdf
O ring seal design guide
O ring seal design guide-FastDash TM Flange Seal Oring Design Guide Enter either the "E" diameter (ie rod diameter) or the "A" diameter (ie bore diameter), Press the "Submit" button, As a result, the appropriate dash no orings will be listed along with their associated groove detailsGeneral Engineering Menu ORings Suppliers Molded ORings Services ORings Design Guidelines, Specifications, Materials An Oring , also known as a packing , is a flexible gasket in the shape of a loop;
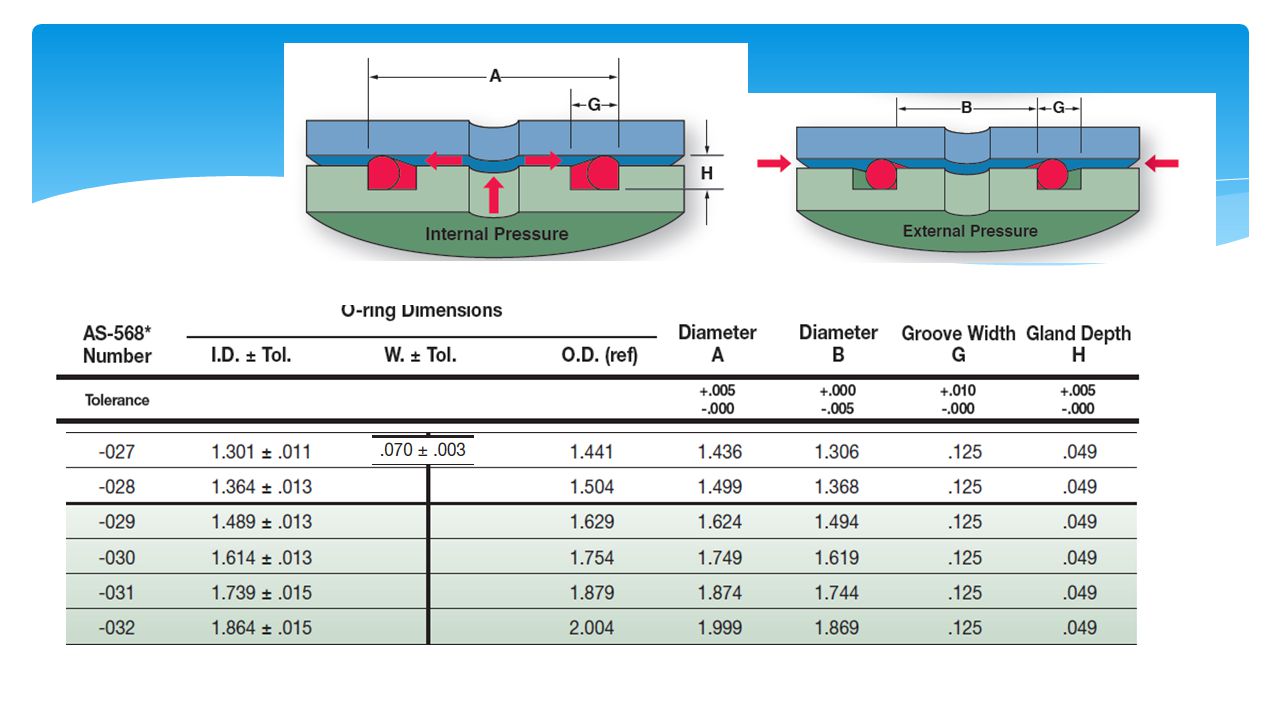



Design Of O Ring Seals Ppt Video Online Download
It is a elastomer with a round crosssection designed to be seated in a groove and compressed during assembly between two or more parts, creating a seal at the interfaceThe squeeze or rate of compression is a major consideration in Oring seal design Elastomers may take up the stackup of tolerances of the unit and its memory maintains a sealed condition Orings with smaller cross sections are squeezed by a higher percentage to overcome the relatively higher groove dimension tolerances 3Rubber Seals, Sealing Devices & ORing Seal Design Apple
Gland Dimensions for Industrial ORing Static Seals, 1035 Bar (1500 psi) Maxt (Continued) ooo 001 001 000 005 000 ORing Size Parker No 2 ID Dimensions w Mean OD (Ren Ring Rings Ring Guide for Design Table 42 Chamfer An le to (X Greater Than Y) X Free Y Oring Chamfer to Serve as Shoe Horn 100 to 0 Cylinc½r gore 100 toSTANDARD AS568B ORING GROOVE DESIGN The three main types of standard groove designs are Industrial Static, also called Radial, Industrial Reciprocating, also called Dynamic, and Face Seals also called Axial or Flange Radial and Dynamic seals require the presence of a diametrical clearance gap for installationRadial Seal Design Guide These products can expose you to chemicals including carbon black (airborne and extracts), antimony trioxide, titanium dioxide, silica (crystalline), di(2ethylhexyl)phthalate, ethylene thiourea, acrylonitrile, 1,3butadiene, epichlorohydrin, toluenediisocyanate, tetra˜uoroethylene, ethylbenzene, formaldehyde,
C24 ORing dimensions for straight thread tube fittings in accordance with AS 568 C25 ORing dimensions for metric thread with conical recess in accordance with ISO 6149 C26 Preferred metric ORing dimensions C3 ORing Seal Sets ORingmetrisch_15indb 3Orings are used in demanding applications like sealing submerged oil rigs to everyday uses like sealing a coffee mug A complete guide to oring sealing would be extensive and is too exhaustive for one blog entry Luckily Parker and Apple Rubber exist and have catalogs of design literature for anyone looking to deep dive into specific designs8 Select the Seal Select the proper QuadRing® Brand size from the Standard Size tableStart by turning to the section of the table for the crosssection size you have selected, and then finding the QuadRing® Brand for the proper size bore or rod (shaft) you are sealing
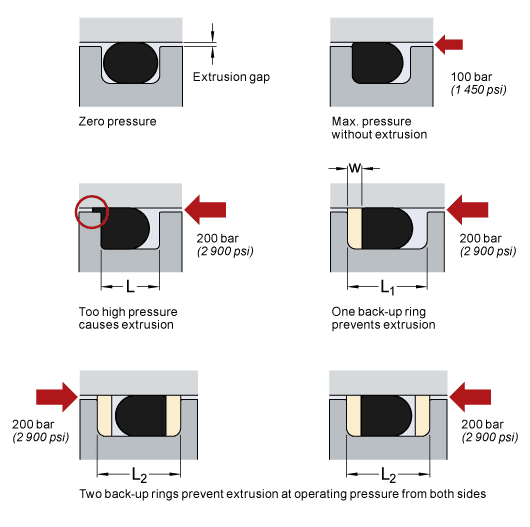



O Rings And Back Up Rings Skf Skf




Oring Ehandbook
This compact, onthejob handbook provides all the practical and theoreticalinformation to design elastomeric Oring seals for the full range of static,reciprocating, and rotary functionsComplete with fully illustrated, detailed examples to guide you stepbystepthrough virtually every seal design situation, Practical Seal Designprovides thorough coverage of ring seal geometry, materialFace Type Seals The face seal design chart below explains the hardware dimensions to use for an Oring seal when the groove is cut into a flat surface For designing systems which contain internal pressure, like the example below, the groove's outside diameter (OD) is primary, and the groove's width then determines the inside diameterORing 5 Dowty O Rings Dowty O Rings was set up in 1961 to produce high volumes of elastomeric ORings With 40 years of experience in producing premium quality elastomeric ORings, Dowty O Rings produces and sells over one billion ORings each year Dowty's expertise lies in providing customised solutions
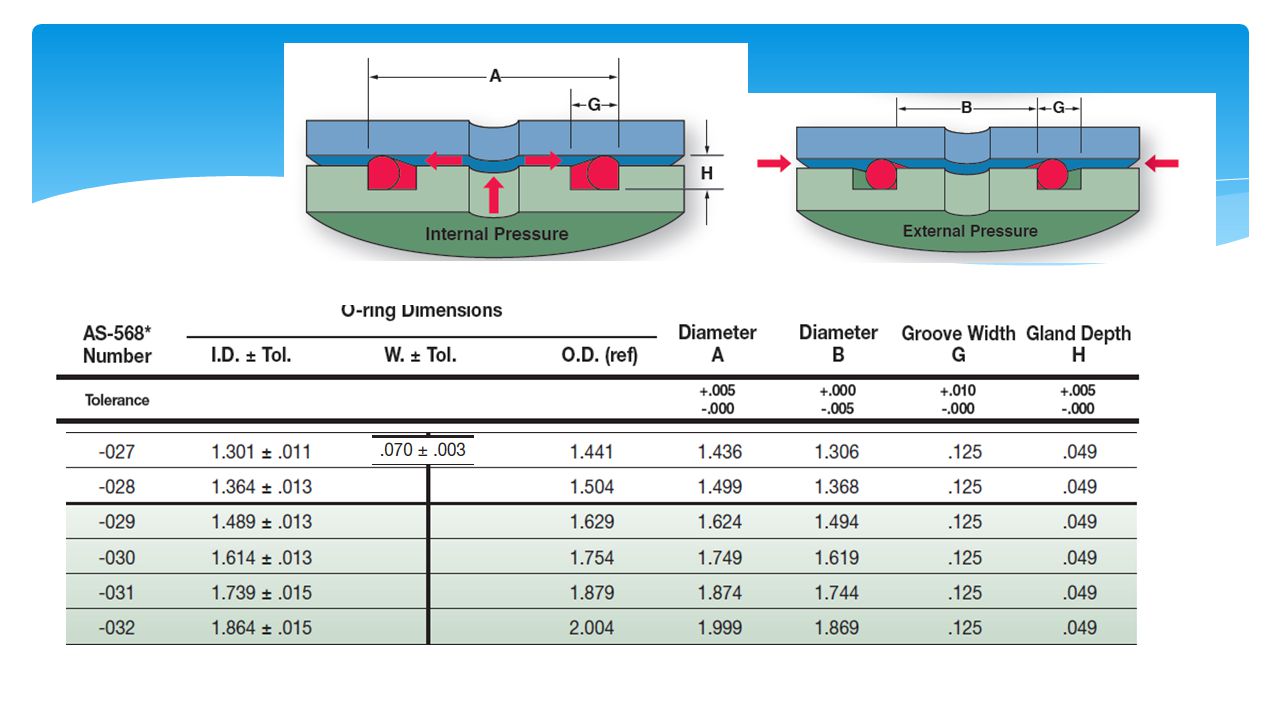



Design Of O Ring Seals Ppt Video Online Download
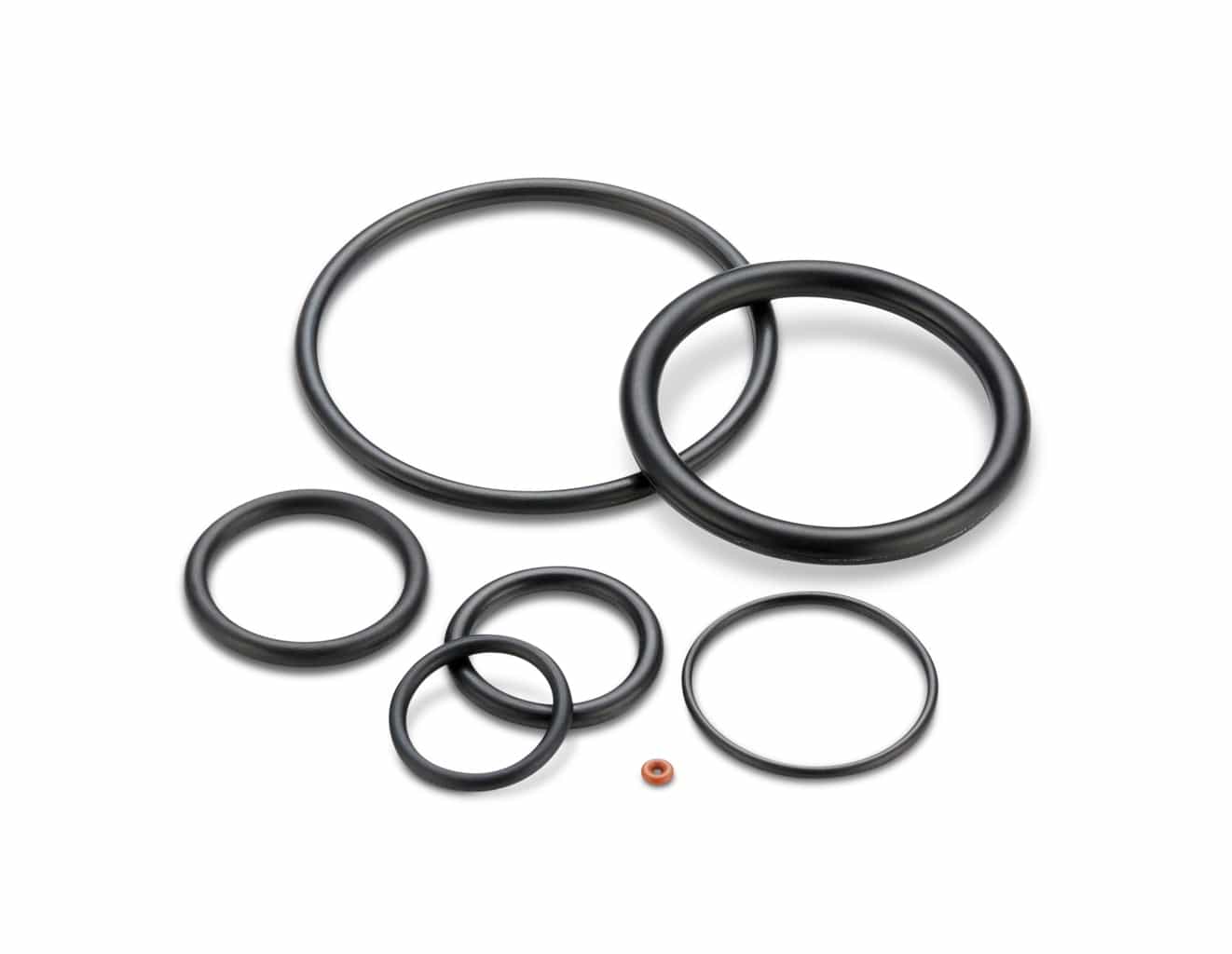



Groove Design O Ring Seals Minnesota Rubber Plastics
A perfectly designed Oring seal is of little use if the Oring is damaged during installation To prevent installation damage for pistontype and rodtype seals, we recommend a 15° chamfer on the bore or rod The Radius Containing Surface Break Edge Sealing Surface Wall Angle Sealing Surface AS568 ORing CS Chamfer Length Series Inches mmCreated Date AM• Select a different Oring hardness • Select a different Oring material with improved coefficient of friction • Increase the groove depth • Consider the use of an alternate design of seal • Viton® has much lower friction than NBR or EPDM or Silicone • Check to ensure squeeze is within the recommended range



Www Pressureseal Com Orings Oguide Pdf
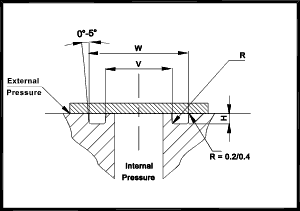



O Ring Seals Roy Mech
FastDashTM Oring Piston Seal Design Guide Enter the "A" diameter (ie bore diameter), Press the "Submit" button, The appropriate dash no orings will beWhen using an oring as part of your seal design, you'll need to design a groove where the oring can sit The great thing is that the groove design remains essentially the same, whether you're sealing two faces, a screw thread, or even a square peg in a round hole (well, the first two are true)The oring seal design process begins with understanding the gland type in which the seal will be seated To ensure the oring fits properly it is recommended that the oring is stretched 1 to 5% circumferential, with ideal stretch at 2%




Seals Eastern O Ring Rod Seal Design Guideline
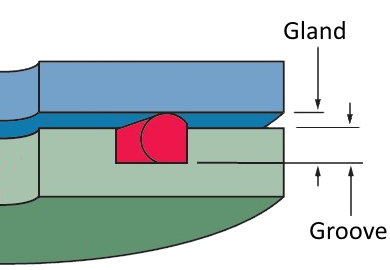



4 Common Mistakes In Designing For An O Ring Axial Face Seal Hot Topics
Rotary ORing Seal Gland Click image above to see design charge, table and guide 54 An Oring has proved to be a practical rotary shaft seal in many applications With the correct design, Parker ORing rotary seal compound N, will provide satisfactory service at surface speeds up to 1500 feet per minuteNow, follow the steps below to design your own oring seal and oring groove Step 1 Choose your rubber properties by going to our Oring Material Guide section Step 2 Make sure that the material you choose will withstand the temperature of your system by going to this rubber temperature range chart Step 3Oring seal The tables at the right and the diagram below provide the recommended gland design parameters In addition, the gland surfaces must be free from all machining irregularities, and the gland edges should be smooth and true and free of nicks, scratches, and burrs A perfectly designed Oring seal is of little use if the Oring
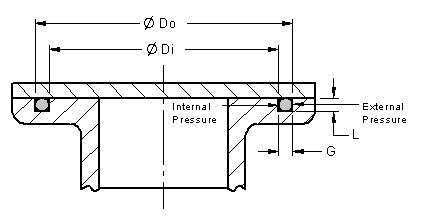



O Ring Installation Design And Specification Static Flange Application Engineers Edge
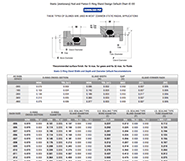



O Ring Groove Design Guides Engineering Quick Reference
0 件のコメント:
コメントを投稿